Maintenance Planner
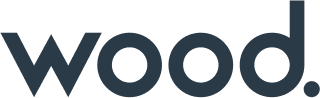
Wood PLC
19 hours ago
Posted date19 hours ago
N/A
Minimum levelN/A
Technicians / ServiceJob category
Technicians / ServiceRESPONSIBILITIES
QUALIFICATIONS
- Describes what needs to be accomplished, estimate labor hours, tools, Spares/components, and resources needed to complete different work orders.
- Uses "quality feedback" from the Site team to optimize the FLOC Task List.
- Reviews PM orders for technical completeness and return PM orders to gatekeeper if not complete Uses, where possible, a FLOC or Global General Task List for basis of actual plan. Follows Plan to Standard (PTS) operating discipline.
- Discuss with Site team for field check and incorporate details in the task list for increase effectiveness.
- When materials availability has been confirmed, store job in active backlog.
- Identify task activities necessary to execute job plan and assign correct work centers.
- Identify materials/tools/equipment required to perform tasks.
- Identify/solicit safety information and requirements necessary to safely perform tasks.
- Performs staffing density checks or staffing limitation checks to validate schedule durations.
- Evaluates schedule deviations to assess schedule impact for proper decision making.
- Progress Measurement Sheet & S Curve progress report preparation for Monitoring & Control of Pit-stops/Turnaround,
- Solicit/Prepare & Review maintenance procedure and ensures all safety and hazard related issues are addressed within the job plan.
- Linking Procedure to Job Package, as applicable in SAP.
- Consider constructability and maintainability when developing plans
- Scheduling - Match the need date with available resources.
- Optimize resource capacity for the highest levels of efficiency and productivity.
- Progress Measurement Sheet & S Curve progress report preparation for Monitoring & Control of Pit-stops/Turnaround,
- Solicit/Prepare & Review maintenance procedure and ensures all safety and hazard related issues are addressed within the job plan.
- Linking Procedure to Job Package, as applicable in SAP.
- Consider constructability and maintainability when developing plans
- Scheduling - Match the need date with available resources.
- Optimize resource capacity for the highest levels of efficiency and productivity.
QUALIFICATIONS
- Engineering Degree in Mechanical or Chemical engineering.
- 8 to 10 years with Operations/ Maintenance of large chemical/ Petro-chemical plants.
- Expertise in SAP Maintenance Modules (PM) with minimum 6 years Hands-on experience.
- Expertise in Primavera P6/ SAP Prometheus with minimum 4 years Hands-on experience.
- Comfortable to collaborate with Diverse Culture & Multinational Site Teams.
- Should be flexible in work timing to match the Site work timing. (Min 4 Hours Overlap of work time)
- Develop/manage Task List
- Develop Job packages
- Effective utilization of available resources
- Use Critical Path Methodology in job plans
- Logical sequencing basics
- Types of Planning constraints
- Know which procedures and specifications are applicable
JOB SUMMARY
Maintenance Planner
Wood PLC
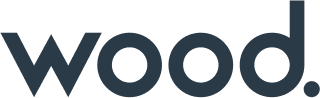
Chennai
19 hours ago
N/A
Full-time